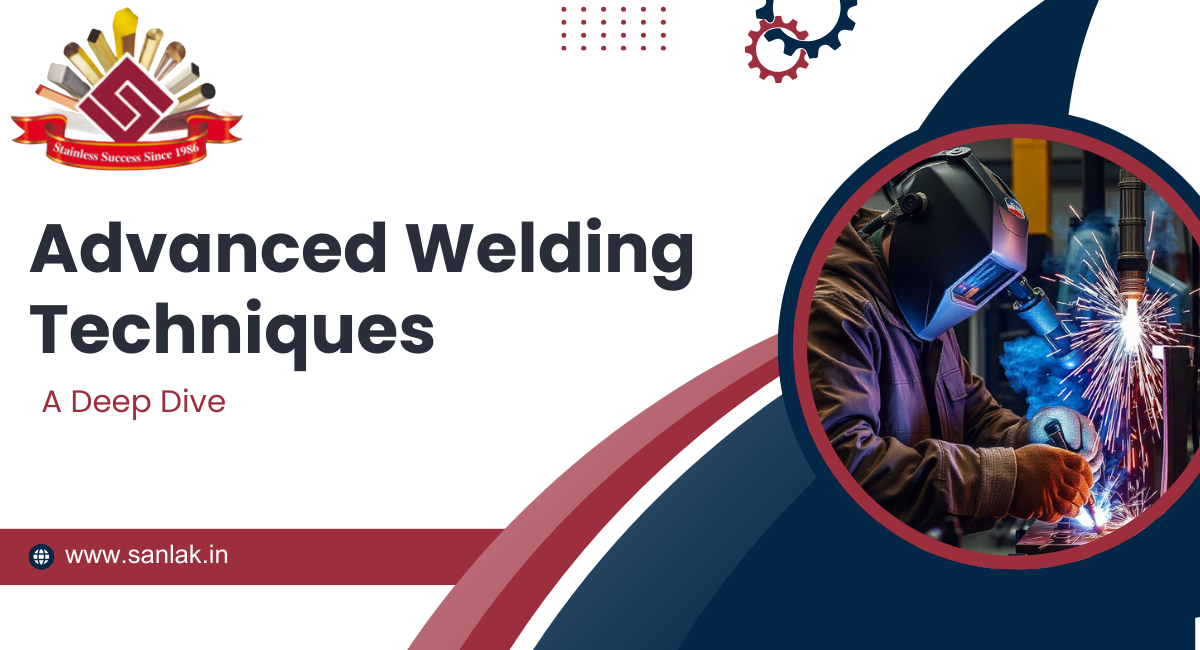
Advanced Welding Techniques: A Deep Dive
Welding is more than just a skill—it’s the force that holds everything together. From the tall buildings that fill city skylines to the tiny parts inside your smartphone, welding is quietly shaping the world around us. For years, traditional methods like TIG, MIG, and Stick welding have been the foundation of manufacturing. But as technology moves forward, a new wave of advanced welding techniques is transforming industries like aerospace, automotive, and more.
In this blog, we’re going to explore the future of welding. Let’s look at how these new techniques are not just improving the way we build things but changing it completely. With amazing precision and faster, more efficient processes, these advancements are paving the way for a new era in manufacturing. Ready to see how welding is evolving? Let’s jump in!
The Basics of Welding (Recap)
Before we dive into advanced welding techniques, let’s quickly go over some of the most common traditional welding methods:
- MIG Welding (Metal Inert Gas): This method uses a continuous wire feed and a shielding gas to create a weld. It’s popular for being fast and easy to use.
- TIG Welding (Tungsten Inert Gas): TIG welding uses a non-consumable tungsten electrode and a shielding gas to create precise, high-quality welds.
- Stick Welding (Shielded Metal Arc Welding): This method uses a consumable electrode coated with flux to protect the weld from contamination.
While these traditional methods are great for many jobs, they may not be ideal for complex or highly precise tasks. That’s where advanced welding techniques come in.
What Makes Welding 'Advanced'?
Advanced welding techniques stand out because they can:
- Achieve higher precision and accuracy: These methods use tools like lasers or electron beams to control the welding process with extreme precision.
- Produce stronger and more durable welds: Advanced welding creates welds that are stronger and last longer.
- Reduce material waste and energy use: These techniques use less material and are more energy-efficient, saving both resources and costs.
- Weld specialized materials: Advanced welding is perfect for joining tough or unusual materials and complex shapes that traditional methods can’t handle.
Industries like aerospace, automotive, and construction require the highest quality, reliability, and efficiency. Advanced welding techniques are crucial to meet these tough standards. By using them, manufacturers can produce high-performance and durable products.
Understanding Advanced Welding Techniques
Laser Welding
Laser welding uses a powerful laser beam to melt and join materials together. This method has several benefits:
- High Precision: The laser can be focused precisely, making the welds very accurate.
- Minimal Heat-Affected Zone (HAZ): The heat is concentrated in a small area, which reduces distortion and helps maintain the material’s properties.
- Deep Penetration: Laser welding can reach deep into thick materials, making it great for tough jobs.
Laser welding is used in industries like:
- Aerospace: Welding strong alloys for airplane parts.
- Automotive: Joining different metals and making complex welds.
- Electronics: Assembling tiny, intricate electronic parts.
Electron Beam Welding (EBW)
EBW uses a focused beam of electrons to melt and join materials in a vacuum. Some key benefits include:
- High-Quality Welds: The electron beam creates clean, strong welds with few defects.
- Narrow Weld Beads: The welds are very narrow, which reduces the need for extra material and minimizes distortion.
EBW is used in industries such as:
- Aerospace: Welding important parts like turbine blades and rocket nozzles.
- Medical Devices: Making precise, sterile medical implants.
- Nuclear Industry: Joining parts in nuclear reactors.
Friction Welding
Friction welding works by rotating one part against another, creating heat from the friction. The heat melts the surface, joining the two parts. This technique has advantages like:
- High Strength: Friction-welded joints are strong and durable.
- Reduced Material Waste: Very little material is wasted during the process.
Friction welding is used in industries such as:
- Automotive: Joining car parts like driveshafts and suspension pieces.
- Railway: Welding railway tracks and other parts.
- Construction: Joining steel beams and other structural components.
Ultrasonic Welding
Ultrasonic welding uses high-frequency vibrations to generate heat and pressure between two parts, joining them together. Some benefits include:
- High-Speed Welding: It’s a fast process, making production more efficient.
- Strong Seals: The technique can create airtight seals, making it ideal for sensitive parts.
Ultrasonic welding is used in industries such as:
- Plastics: Joining plastic parts in different products.
- Electronics: Assembling small electronic parts and packaging them.
- Medical Devices: Making disposable medical devices.
These advanced welding techniques are transforming industries by offering stronger, faster, and more precise ways to create and join parts. Whether in aerospace, automotive, or medical fields, these methods are making manufacturing better and more efficient.
Advanced Welding Techniques in Specific Industries
Aerospace Industry
The aerospace industry needs the best quality, reliability, and lightweight materials. Advanced welding techniques help meet these high demands:
- Laser Welding and EBW: These techniques are used to weld strong materials like titanium and aluminium, ensuring accurate and strong welds.
- Case Study: Laser welding has been used to make aircraft engine parts lighter and more efficient, improving their overall performance.
Automotive Industry
The automotive industry aims to make vehicles lighter and more fuel-efficient. Advanced welding helps achieve these goals:
- Friction Welding: This method joins different materials, like steel and aluminium, helping reduce weight and increase strength.
- Laser Welding: Laser welding is used to create complex joints and reduce distortion in car parts.
- Example: Laser welding has helped make car bodies lighter, improving fuel efficiency and reducing emissions.
Medical Device Industry
In the medical device industry, precise and sterile welding is essential for patient safety:
- Ultrasonic Welding: This technique is often used to join plastic parts in medical devices, creating strong, airtight seals.
- EBW: EBW is used to make high-precision medical implants and surgical tools, reducing contamination and ensuring top performance.
- Case Study: Ultrasonic welding is used to produce disposable syringes quickly and with high-quality results.
Construction Industry
In construction, advanced welding techniques help improve speed and durability:
- Friction Welding: This method is used to join large steel parts, speeding up construction and reducing labor costs.
- Future Trends: The use of robotic welding systems and AI-powered welding processes is expected to further boost efficiency and quality in construction.
By understanding the specific needs of each industry, engineers can choose the right welding technique to improve product quality, reduce costs, and meet high standards.
The Future of Welding: Emerging Technologies
The welding industry is always changing, driven by new technology. Let’s look at some emerging technologies that are shaping the future of welding:
Additive Manufacturing (3D Printing)
3D printing is changing how products are designed and made. When combined with welding, it can create complex shapes that would be hard or impossible to make with traditional methods.
Benefits:
- Design Flexibility: 3D printing allows for creating detailed and complex designs.
- Less Material Waste: Only the material needed is used.
- Faster Prototypes: You can make prototypes quickly.
Challenges:
- Material Limitations: Not all materials work well with 3D printing and welding.
- Post-Processing: Printed parts may need extra work, like heat treatment or machining.
Robotic Welding
Robotic welding systems have many benefits:
- More Precision: Robots can weld very accurately, without mistakes.
- Better Quality: With fewer errors, the welds are of higher quality.
- Improved Safety: Robots can handle risky tasks, keeping workers safe.
- Higher Productivity: Robots can work around the clock, increasing production speed.
AI and Machine Learning in Welding
AI and machine learning are making big changes in welding by:
- Predictive Maintenance: AI can predict when equipment might break, helping to reduce downtime.
- Better Quality Control: AI vision systems can inspect welds for defects, ensuring they’re perfect.
- Smarter Welding: AI can adjust welding settings in real time to improve efficiency and lower costs.
As these technologies keep advancing, the future of welding looks bright. By embracing these innovations, the welding industry can tackle challenges and improve manufacturing across many sectors.
Conclusion
Advanced welding techniques have transformed manufacturing, offering better quality, strength, and complexity for industries like aerospace, automotive, medical devices, and construction.
With emerging technologies like 3D printing, robotic welding, and AI, the future of welding is full of potential. By staying updated and embracing these innovations, we can unlock new possibilities and shape a brighter future for manufacturing.
For the best welding products and advanced techniques, consider Santhana Lakshmi Metals, a leading manufacturer and supplier in India.