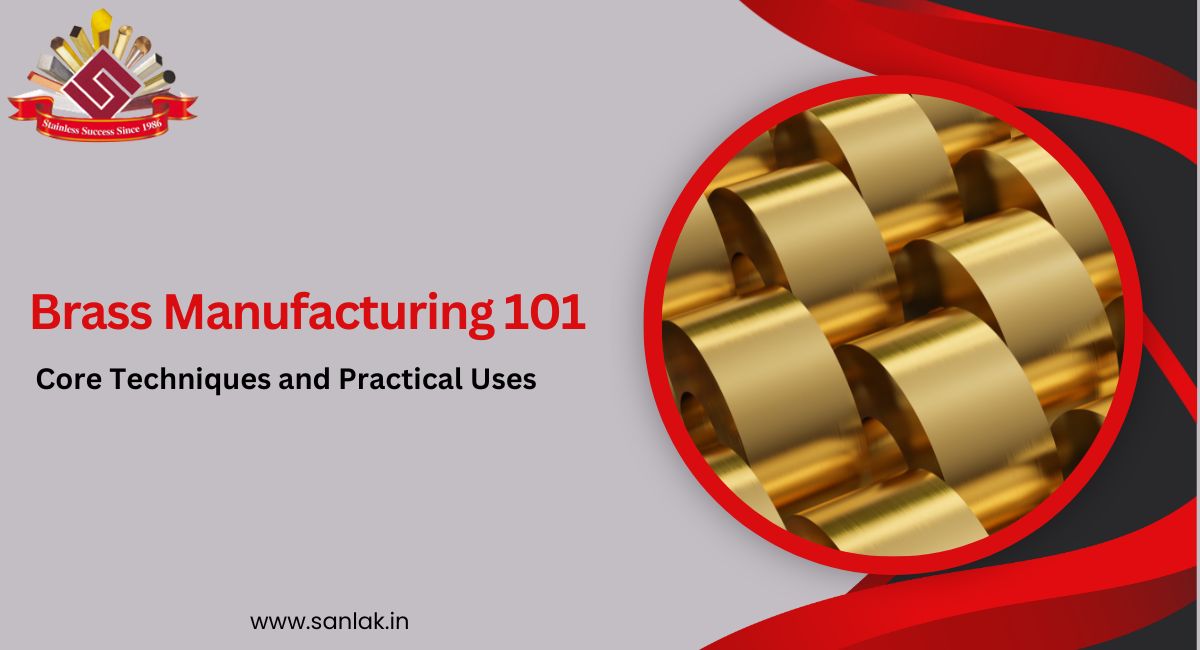
Brass Manufacturing 101: Core Techniques and Practical Uses
Introduction to Brass Manufacturing
What is Brass?
Brass is an alloy made primarily of copper and zinc, and it plays a vital role in brass manufacturing. Known for its warm, golden color and excellent durability, brass is a preferred choice in various applications. Depending on its intended use, brass can also include small amounts of other metals, such as lead, to enhance specific properties. This versatile material is prized for its workability, corrosion resistance, and acoustic qualities, making it ideal for products ranging from musical instruments to plumbing fixtures.
Importance of Brass in Industry
Brass manufacturing is essential across many industries for several reasons:
- Durability and Longevity: Products made from brass are resistant to wear and tear, which is crucial in brass manufacturing. This durability means that items require fewer replacements, saving time and resources in the long run.
- Corrosion Resistance: One of the key advantages of brass in brass manufacturing is its ability to resist rust and corrosion. This property is particularly valuable in plumbing and marine applications where exposure to moisture is common.
- Acoustic Quality: Brass is widely used in musical instruments due to its exceptional acoustic properties. In brass manufacturing, instruments like trumpets, trombones, and saxophones rely on brass for their rich, resonant tones.
- Aesthetic Appeal: The attractive appearance of brass makes it a popular choice in brass manufacturing for decorative items and fixtures. From jewelry to architectural hardware, the warm glow of brass enhances the beauty of various designs.
- Versatility: Brass can be easily machined, cast, and shaped, allowing for a diverse range of products in brass manufacturing. This adaptability ensures that brass remains relevant in sectors such as automotive, electrical, and architecture.
The Brass Manufacturing Process
Overview of the Production Steps
The brass manufacturing process involves several key steps to transform raw materials into finished products. Here’s a simple overview:
- Material Selection: The process begins with choosing the right raw materials, typically copper and zinc. Depending on the desired properties of the final product, other metals may also be added.
- Melting: The selected metals are melted together in a furnace at high temperatures. This creates a molten alloy, which allows for uniform mixing.
- Casting: The molten brass is poured into molds to create specific shapes. This step is crucial for forming the basic structure of the final product, whether it’s a sheet, rod, or a complex component.
- Machining: Once the brass has cooled and solidified, it undergoes machining. This involves cutting, drilling, and shaping the brass to meet precise specifications. Machining ensures that the final product fits perfectly for its intended application.
- Finishing: After machining, the brass pieces are polished and treated to enhance their appearance and corrosion resistance. This can include processes like plating or applying protective coatings.
- Quality Control: Finally, each brass product undergoes rigorous quality control checks. This step ensures that all items meet industry standards for durability, performance, and aesthetic appeal.
Raw Materials Used
The primary raw materials used in brass manufacturing include:
- Copper: The main component of brass, copper provides strength, conductivity, and resistance to corrosion. It’s typically sourced in various grades, depending on the desired properties of the alloy.
- Zinc: This metal is added to copper to create brass. Zinc improves the malleability and workability of the alloy, making it easier to shape and form during the manufacturing process.
- Alloying Elements: In addition to copper and zinc, small amounts of other metals may be added to achieve specific characteristics. Common alloying elements include:
- Lead: Often added to improve machinability, especially in industrial applications.
- Tin: Enhances corrosion resistance and strength.
- Nickel: Improves hardness and provides a shiny finish.
Understanding the brass manufacturing process and the raw materials involved helps to appreciate the craftsmanship and complexity behind creating this versatile alloy. From musical instruments to plumbing fixtures, the quality of brass products is directly tied to the meticulous steps taken during manufacturing.
Core Techniques in Brass Manufacturing
Casting: Creating Brass Shapes
In brass manufacturing, casting involves pouring molten brass into molds to create specific shapes. This technique is great for making complex designs and allows for producing many items at once.
Machining: Precision Shaping and Finishing
Machining in brass manufacturing is the process of cutting and shaping solid brass pieces to exact sizes. Tools like lathes and mills are used to ensure that each part fits perfectly for its intended use.
Extrusion: Shaping Brass into Long Forms
Extrusion is a brass manufacturing method where heated brass is pushed through a die to create long shapes, such as rods or tubes. This technique produces uniform thickness, making it efficient for elongated components.
Forging: Strengthening Brass Components
Forging in brass manufacturing involves heating brass and shaping it using force, such as hammers or presses. This process strengthens the brass, making it more durable and suitable for demanding applications.
Quality Control in Brass Manufacturing
Ensuring Consistency and Durability
In brass manufacturing, quality control is crucial to ensure that every product meets high standards. This involves checking that the brass is consistent in composition and performance. Consistency helps guarantee that each item will function properly and last over time.
Testing Methods and Standards
Brass manufacturing relies on various testing methods to assess quality. Common tests include:
- Visual Inspections: Checking for surface defects and imperfections.
- Dimensional Checks: Measuring parts to ensure they match specified sizes.
- Strength Tests: Assessing the durability and resistance of the brass under stress.
These tests help ensure that the final products are reliable and meet industry standards. Quality control is vital in brass manufacturing to maintain customer satisfaction and product excellence.
Practical Applications of Brass
Musical Instruments: The Sound of Brass
Brass manufacturing plays a vital role in creating musical instruments like trumpets, trombones, and saxophones. The unique properties of brass allow these instruments to produce rich, resonant tones, making them favorites among musicians.
Plumbing and Fixtures: Why Brass is Preferred
In brass manufacturing, plumbing components and fixtures are often made from brass due to its excellent corrosion resistance and durability. Brass plumbing parts can withstand high pressure and exposure to moisture, making them a reliable choice for water systems.
Decorative Items: Aesthetic and Functional Uses
Brass manufacturing is also key in producing decorative items, such as jewelry, lighting fixtures, and hardware. The warm, golden hue of brass adds beauty to various designs, while its strength ensures that these items are both aesthetically pleasing and functional.
Overall, brass manufacturing provides essential materials that enhance both performance and aesthetics in many everyday applications.
Future Trends in Brass Manufacturing
Innovations in Techniques
The future of brass manufacturing is seeing exciting new technologies. Automation and advanced machines are making production faster and more precise. Techniques like 3D printing are also emerging, allowing for more complex designs that were hard to create before. These innovations help improve quality and reduce costs
Market Demand and Developments
The demand for brass products is on the rise, driven by various industries. There’s a growing focus on sustainability, leading to more eco-friendly brass manufacturing methods. Many companies are also using recycled brass, which conserves resources and appeals to consumers who prefer sustainable options.
Conclusion
Brass manufacturing plays a crucial role in creating a versatile alloy made from copper and zinc. Known for its durability, corrosion resistance, and attractive appearance, brass is widely used in products like musical instruments, plumbing fixtures, and decorative items. Companies like Sanlak are at the forefront of this industry, focusing on high-quality production and innovative practices. The manufacturing process involves carefully selecting materials, melting, casting, machining, and strict quality control to ensure top standards. With advancements in technology and a focus on sustainability, brass manufacturing is evolving to meet modern demands, ensuring that brass remains an essential material in various industries for years to come.