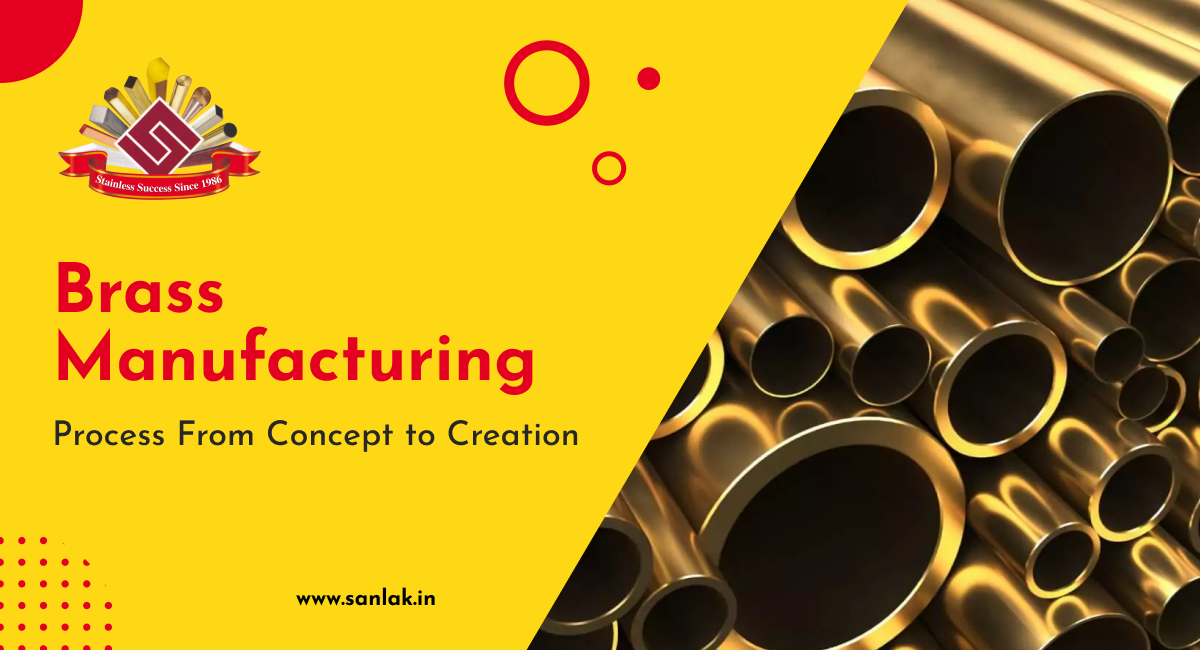
Brass Manufacturing Process From Concept to Creation
A Golden History: Brass has been valued for centuries. Ancient Romans used it for coins, Greeks for ornaments, and during the period of artistic and cultural rebirth, it became popular for musical instruments. Its durability and beauty have made it a key material in many cultures and industries.
Modern Era
In the modern era, brass continues to shine with its remarkable versatility. Today, it’s found in:
Plumbing and Electrical Systems: Brass’s resistance to corrosion and excellent strength make it ideal for fixtures, valves, and connectors.
Musical Instruments: Its acoustic properties ensure rich, warm sounds in trumpets, trombones, and saxophones.
Decorative and Architectural Elements: Brass adds a touch of elegance and durability to everything from door handles and railings to intricate design features.
Brass’s blend of functionality and beauty ensures it remains a popular choice in both practical and artistic fields.
Ready to Dive In?
Explore how brass products are made, from concept to creation. This article will guide you through the process, making it interesting and informative for history enthusiasts, hobbyists, and curious minds alike.
From Dream to Design: Bringing Ideas to Life
Turning a brass product from a simple idea into a finished item involves a creative and technical journey:
- From Idea to Blueprint: It starts with developing initial concepts and sketching them out. Designers then translate these ideas into detailed blueprints, outlining every aspect of the product.
- CAD Modeling:Computer-Aided Design (CAD) software brings these blueprints to life. CAD models provide a precise, 3D visualization of the product, allowing for detailed adjustments and refinements.
- Prototyping:Once the digital model is complete, a prototype is created. This physical version helps test and validate the design before full-scale production. Prototyping ensures the final product will meet expectations in terms of form, fit, and function.
This process transforms abstract ideas into real, functional brass products, blending creativity with cutting-edge technology.
Transforming Vision into Reality: The Manufacturing Process
The magic happens when the design meets the manufacturing floor. Brass, a blend of copper and zinc, is melted into a liquid form and then transferred into molds to create the basic shape. This process, called casting, is the foundation for countless brass products.
Once cast, the brass undergoes a transformation. It's shaped, refined, and perfected through techniques like forging, where it’s pressed into desired shapes, and machining, where exact tools shape the detailed features. The final touch involves polishing and finishing, highlighting the brass’s natural shine and ensuring its durability.
Ensuring Excellence: Quality Control in Brass Manufacturing
Inspection and Testing:
- Visual Checks: Looking for any defects.
- Strength Tests: Ensuring the brass is durable and performs well.
Statistical Process Control (SPC):
- Monitoring: Using data to keep the manufacturing process consistent and spot problems early.
Meeting Industry Standards:
- Certifications: Testing to make sure products meet safety and quality standards.
- Regulations: Following rules to ensure products are reliable and safe.
Brass and the Planet
We're committed to making brass in a way that's kind to our planet. Here’s how:
- Recycling Brass and Reducing Waste: We turn old brass products into new ones, saving energy and reducing waste. This means less mining for new materials and less trash in landfills.
- Energy Efficiency: We're always looking for ways to use less energy in our factories. This includes using energy-efficient machines, recycling heat, and finding smarter ways to power our operations.
- Eco-Friendly Processes: We're careful about the chemicals we use and how we dispose of waste. We also work hard to reduce water usage in our processes.
Brass: The Future is Now!
Additive Manufacturing (3D Printing):
What It Is: Picture a 3D printer creating a brass part layer by layer, just like building a sculpture from scratch. This technology allows for designing and producing complex brass components with less waste and more creativity. You can now make custom parts quickly and easily, transforming how we think about brass manufacturing.
Smart Manufacturing and Industry 4.0
What It Is: Imagine factories that are as smart as your smartphone. Smart manufacturing uses high-tech tools and sensors to keep an eye on every part of the production process. Industry 4.0 connects machines and data to make everything run smoother, faster, and more accurately. This means fewer mistakes, better quality, and more efficient production.
These cutting-edge technologies are setting the stage for a new era in brass manufacturing, where innovation leads to smarter, more flexible, and eco-friendly production methods.
Conclusion
From ancient times to today, brass has been a versatile and valuable material, it’s journey starts with design and material selection, followed by melting, casting, and machining. The process ends with careful finishing to ensure high quality and performance. This blend of tradition and innovation showcases how brass continues to shape modern products and industries.
Share the magic of brass with your friends! Let them explore the incredible journey from raw materials to finished products, And don’t forget to check out Sanlak for more insights into brass manufacturing and other industry trends!