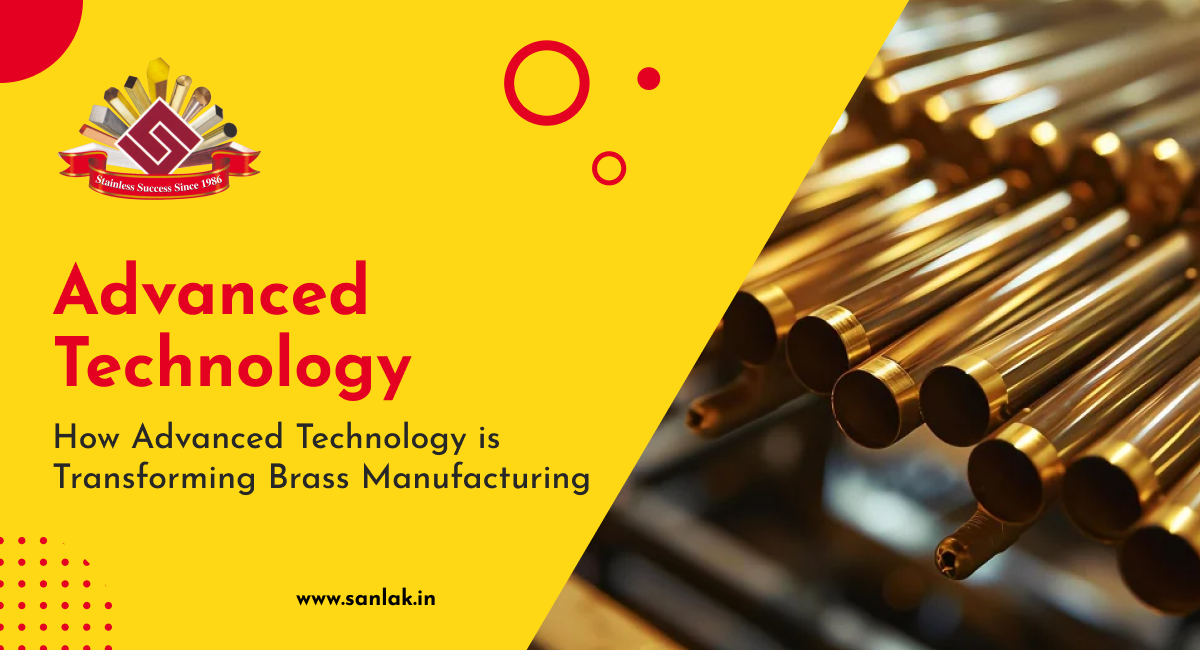
How Advanced Technology is Transforming Brass Manufacturing
The Brass Industry: A Quick Look
Brass has been used for hundreds of years because it's strong, resists rust, and looks good. It's found in things like musical instruments, home decor, plumbing parts, and electrical systems. Despite its long history, the way brass is made hasn't changed much—until now.
Why Technology is Needed
In today’s world, industries need to keep up with fast-changing demands. The brass industry faces challenges like the need for high-quality products, sustainable practices, and lower costs. Using new technology isn’t just a choice; it’s a must for staying in business and growing. Advanced technology can change how brass is made, making the process faster, more precise, and eco-friendly. This not only helps meet today’s needs but also prepares the industry for the future, keeping it strong and competitive.
Robots on the Job: Automation in Brass Manufacturing
Automation is no longer a futuristic concept. It's here, and it's transforming the brass industry. From the casting floor to the machining center, robots are taking on tasks, increasing efficiency, and ensuring precision like never before.
Robots do repetitive jobs like assembling, polishing, and checking products. They work quickly and consistently, and can keep going without breaks, boosting production.
Automation in Casting and Machining: Automated systems manage casting (pouring molten brass into molds) and machining (cutting and shaping). These systems are very precise, making each piece exactly right and reducing mistakes.
Printing the Future: 3D Brass Manufacturing
Forget traditional molds and casting. 3D printing is revolutionizing the way we create brass products. From intricate designs to complex shapes, this technology is opening up a world of possibilities.
How It Works
- Design: Engineers create a digital model of the brass part.
- Printing: The 3D printer builds the part layer by layer using brass material.
- Finishing: The printed part may need some final touches, like polishing.
Benefits
- Complex Designs: Create detailed shapes that are hard to make with traditional methods.
- Customization: Easily modify designs for custom parts.
- Less Waste: Uses only the material needed, reducing waste.
- Faster Production: Speeds up making and testing new parts.
AI and Machine Learning: Brass Manufacturing's New Toolbox
AI and machine learning are bringing intelligence to the brass manufacturing process. These smart technologies are transforming how we work.
Optimizing Production: AI analyzes data to find the best ways to make brass, cutting waste and speeding up production.
Predicting Problems: Machine learning forecasts equipment failures, preventing costly downtime. It's like having a crystal ball for your machines.
From design to delivery, AI and machine learning are shaping the future of brass.
IoT: Smart Factories, Smarter Brass
The Internet of Things (IoT) is transforming how brass is made. By connecting machines and systems, factories are becoming smarter and more efficient.
See It All, Control It All: IoT gives you a real-time view of your entire operation, from start to finish.Less Downtime, More Profit: Predict when machines might fail, so you can fix them before they break.
IoT is the key to a more connected and efficient brass industry.
Case Studies Examples
Let's see how top brass manufacturers are using technology to shine. From factory floors to the bottom line, these success stories will inspire and inform.
Success Stories from the Industry
Efficiency Boost: A brass plumbing parts manufacturer adopted automation and robotics, which led to a 30% increase in production speed and a 20% reduction in material waste. The robots handled repetitive tasks, allowing skilled workers to focus on more complex jobs.
Predictive Maintenance: An electrical component manufacturer used predictive maintenance powered by AI. They reduced machine downtime by 40% because the AI predicted when parts would fail and scheduled maintenance before any issues occurred.
Sustainable Practices: A brass decorative items company used advanced recycling technology to reuse scrap brass. This reduced their raw material costs by 25% and lowered their environmental impact.
Future Trends in Brass Manufacturing
Emerging Technologies to Watch
- Smart Factories: Connected systems using IoT and AI for better efficiency and quality.
- Advanced Materials: New, stronger, and lighter brass alloys.
- Augmented Reality (AR): Real-time guidance for workers to improve productivity.
- Sustainable Practices: Better recycling and energy-efficient processes.
Predictions for the Next Decade
- Increased Automation: More robots handling complex tasks, freeing up human workers.
- AI-Driven Decisions: AI optimizing operations and supply chains.
- Customization: More flexible and customized products with 3D printing.
- Global Collaboration: Companies sharing data and resources for innovation.
Conclusion
Advanced technology is making brass manufacturing faster and more efficient with automation, 3D printing, AI, and IoT, these innovations not only meet today’s demands but also pave the way for future growth. The brass industry is set for a bright future, driven by continuous improvement and innovation.
If you found this article insightful, consider sharing it with others who might benefit. And if you’re looking for top-notch brass manufacturing solutions, companies like Sanlak are leading the way in integrating these advanced technologies.