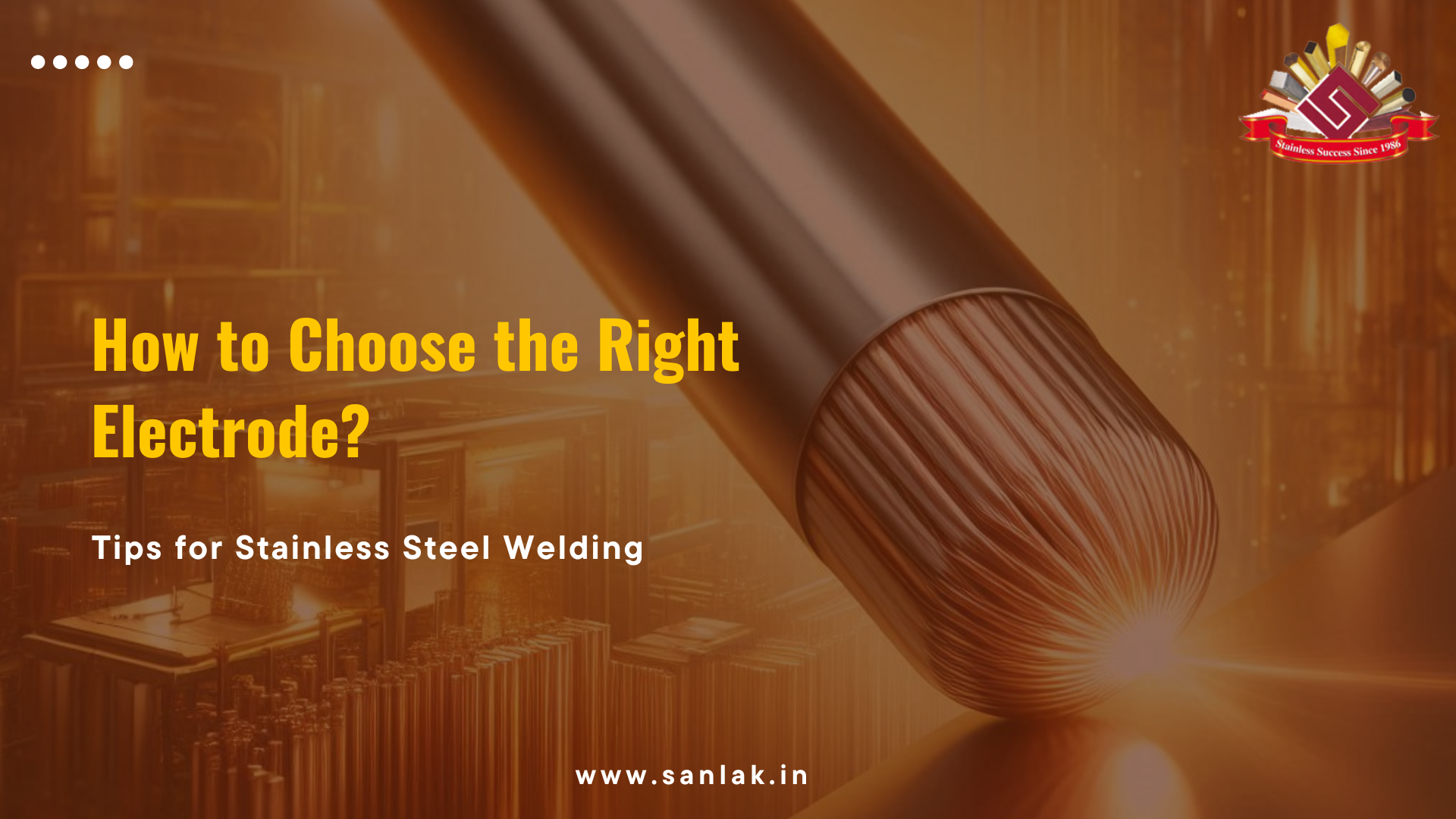
How to Choose the Right Electrode for Stainless Steel Welding ?
Stainless steel welding plays an important role in many industries, like construction and manufacturing. It involves joining stainless steel parts to build structures, machines, and various products. The strength and durability of these welded joints are crucial for the overall performance and safety of the final product.
One of the most important factors in getting a good weld is picking the right electrode. The electrode is a filler material that also helps carry the electrical current needed for welding. It affects how the weld looks, how strong it is, and how well it resists rust. By selecting the right electrode, you can make sure your Stainless Steel welds are strong, neat, and long-lasting.
Understanding Stainless Steel Welding
Stainless steel is a popular alloy known for its strength, resistance to rust, and shiny look. However, these same qualities can make welding stainless steel a bit tricky.
One challenge is its high chromium content, which creates a protective layer that can get in the way during welding. Also, stainless steel doesn’t conduct heat well, which means it can warp or crack if not welded carefully.
Here are some common stainless steel types used in welding:
- Type 304: A flexible alloy that resists rust and is easy to shape.
- Type 316: Offers better rust protection, especially in environments with salt, like coastal areas.
- Type 309: Known for its resistance to heat and easy welding.
- Type 310: Contains more nickel, making it great for high temperatures and tough environments.
The type of stainless steel you're using will affect which electrode to choose. For example, if you’re welding Type 316, you’ll need electrodes with more nickel to match the alloy and make a strong, high-quality weld.
Types of Electrodes for Stainless Steel Welding
MIG (Metal Inert Gas) Electrodes MIG welding, also known as gas metal arc welding (GMAW), is a common way to weld stainless steel. In this process, a continuous wire electrode is fed into the weld, and a shielding gas protects it from contamination.
Common MIG electrodes for stainless steel:
- ER308L: A low-carbon electrode that’s good for general-purpose welding.
- ER309L: A high-chromium electrode that provides excellent resistance to rust and heat.
TIG (Tungsten Inert Gas) Electrodes TIG welding, or gas tungsten arc welding (GTAW), is a precise method that uses a tungsten electrode to create an arc. Like MIG, it also uses shielding gas to protect the weld from contamination.
Common TIG electrodes for stainless steel:
- 2% Thoriated: A tungsten electrode with 2% thoria, which gives it stable arcs and helps with electron flow.
- 2% Ceriated: Similar to thoriated electrodes but uses ceria instead of the radioactive thorium, making it safer.
Stick (Shielded Metal Arc Welding) Electrodes Stick welding, or shielded metal arc welding (SMAW), uses a coated electrode that melts to create the weld. The coating provides a protective shield to prevent contamination.
Common Stick electrodes for stainless steel:
- E308L: A low-carbon electrode for general-purpose stainless steel welding.
- E309L: A high-chromium electrode that resists both rust and heat.
The right electrode depends on the type of stainless steel, the shape of the weld, and the properties you need in the final weld.
Factors to Consider When Choosing an Electrode for Stainless Steel Welding
Choosing the right electrode for welding stainless steel is crucial to ensure a strong, clean, and durable weld. Here are some key factors to consider, explained in simple terms:
1. Type of Stainless Steel
Different types of stainless steel have different chemical makeups, so it's important to match the electrode to the specific type of stainless steel you're welding.
For example:
If you're welding Type 316 stainless steel, you'll need an electrode that contains more nickel to match its composition. This ensures a strong, high-quality weld.
2. Welding Position
The position in which you're welding (like flat, vertical, or overhead) can affect the choice of electrode. Some positions are easier to weld in than others, and certain electrodes are better suited for different positions:
- Flat position: This is the easiest position to weld in, so you have more flexibility in choosing your electrode.
- Horizontal position: You may need an electrode that helps remove slag easily, which can prevent defects in the weld.
- Vertical position: Use an electrode that keeps a stable arc and avoids burning through the metal.
- Overhead position: Choose electrodes that control the flow of molten metal well and prevent defects in the weld.
3. Welding Process
The type of welding process you’re using also affects the choice of electrode. Each process requires different types of electrodes:
- MIG welding: Uses a continuous wire electrode.
- TIG welding: Uses a non-consumable tungsten electrode and requires a shielding gas.
- Stick welding: Uses coated electrodes that melt as you weld.
Each process works best with specific electrode types, so choose accordingly.
4. Desired Weld Properties
Think about what you want from the final weld. What kind of strength, corrosion resistance, and appearance do you need?
- Strength: Choose an electrode that will create a strong weld with the needed durability and flexibility.
- Corrosion resistance: Make sure the electrode matches the stainless steel’s resistance to rust to ensure a long-lasting weld.
- Appearance: Consider how the weld will look. If appearance is important, choose an electrode that gives a smooth, clean weld bead.
Tips for Choosing the Right Electrode for Stainless Steel Welding
Selecting the right electrode for your stainless steel welding project is important to achieve strong, clean welds. Here are some simple tips to guide you:
Check Manufacturer Recommendations
- Always follow the manufacturer’s advice for the electrode. They provide clear details on which stainless steel types, welding positions, and amperage settings work best.
Think About the Job
Consider what the welded part will be used for.
- For food processing, you’ll need electrodes that resist rust.
- Forchemical plants, you might need ones that provide extra strength.
Test Before You Start
- Try out different electrodes on scrap stainless steel before starting your project. This helps you see how the weld looks, how easy it is to use, and how strong it is.
Choose Reliable Suppliers
- Make sure to buy your electrodes from a trusted source. Santhana Lakshmi Metals offers the best stainless steel welding electrodes across the country, ensuring high-quality and durable welds for any project.
By following these tips and choosing the right supplier, you can ensure great welding results!
Common Mistakes to Avoid in Stainless Steel Welding
When choosing and using electrodes for stainless steel welding, avoid these common mistakes to ensure better results:
1. Using the Wrong Electrode
Using electrodes that don’t match the stainless steel alloy can weaken the weld and reduce corrosion resistance.
2. Not Following Process Requirements
Each welding process (MIG, TIG, Stick) needs specific electrodes. Ignoring this can make it hard to keep a stable arc and control the weld.
3. Poor Electrode Storage
Exposing electrodes to moisture or contaminants can damage them, leading to poor weld quality. Store and handle them properly.
Conclusion
Choosing the right electrode is key to achieving strong and long-lasting stainless steel welds. By considering the type of stainless steel, the welding process, and avoiding these common mistakes, you’ll get better welds every time.
For more tips and expert advice don’t forget to check out our blog for more welding tips and insights!