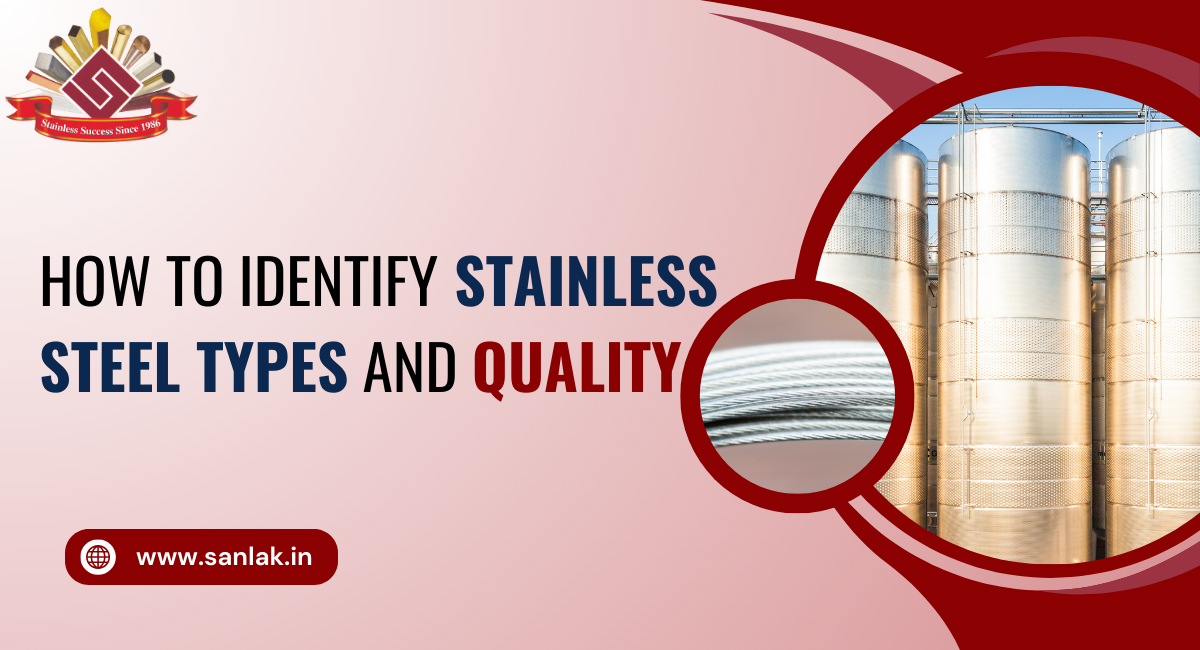
How to Identify Stainless Steel Types and Quality
Introduction
Stainless steel types are available in different grades, each with unique properties and strength. In this blog, you will learn how to check the quality of stainless steel, understand its grades and hardness, and compare 304 vs 316 stainless steel. This guide will help you choose the right stainless steel alloy types for your needs.
How to Check the Quality of Stainless Steel
Checking the quality of stainless steel starts with a visual inspection. High-quality stainless steel types should have a smooth, uniform surface without cracks, rust, or discolouration. Poor-quality stainless steel may show signs of pitting or corrosion, indicating lower resistance to moisture and chemicals. A simple scratch test can also help, as premium stainless steel is highly resistant to scratches and dents.
Another method to test the quality of stainless steel is by checking its chemical composition. A reliable way to do this is through a spectrometer test, which detects elements like chromium, nickel, and molybdenum. These elements define different stainless steel types, with higher chromium and nickel content improving corrosion resistance. Additionally, the stainless steel hardness test helps measure strength, ensuring the material meets industry standards.
Types of Stainless Steel and Their Properties
There are several types of stainless steel, each designed for specific applications. The most common types are austenitic, ferritic, martensitic, duplex, and precipitation-hardening stainless steel. These types differ in composition, strength, and resistance to corrosion, making them suitable for different industries.
Austenitic Stainless Steel – This is the most widely used stainless steel type, known for its excellent corrosion resistance and non-magnetic properties. It contains high levels of chromium and nickel, which enhance durability and flexibility.
Ferritic Stainless Steel – Contains less nickel than austenitic steel, making it more affordable. It provides good strength, oxidation resistance, and magnetic properties, making it suitable for automotive parts and kitchen appliances.
Martensitic Stainless Steel – Known for its high stainless steel hardness and strength. It can be hardened by heat treatment, making it ideal for tools, knives, and turbine blades.
Duplex Stainless Steel – Combines the properties of austenitic and ferritic steel, offering high strength and superior corrosion resistance. It is used in chemical processing, oil refineries, and structural components.
Precipitation-Hardening Stainless Steel – Contains added elements like copper and aluminium, which improve toughness and wear resistance. It is commonly used in aerospace, nuclear industries, and high-performance mechanical components.
Difference Between 304 vs 316 Stainless Steel
Both 304 and 316 stainless steel are austenitic grades, but their composition makes them suitable for different environments. 304 stainless steel contains 18% chromium and 8% nickel, providing excellent corrosion resistance and durability. On the other hand, 316 stainless steel has around 16% chromium, 10% nickel, and 2% molybdenum, which enhances its resistance to saltwater, acids, and harsh chemicals.
When comparing 304 vs 316 stainless steel, the presence of molybdenum in 316 stainless steel gives it superior protection against pitting and crevice corrosion, making it ideal for marine, medical, and chemical industries. Meanwhile, 304 stainless steel is commonly used in kitchen equipment, food processing, and construction due to its strong corrosion resistance and affordability. While both offer durability, 316 stainless steel is preferred for applications exposed to extreme environments.
Another key difference between 304 and 316 stainless steel is their strength and cost. 316 stainless steel has higher tensile strength and better heat resistance, making it more durable for high-pressure applications. However, it is also more expensive than 304 stainless steel, which is why many industries choose 304 stainless steel when high corrosion resistance is not a priority.
Stainless Steel Grades and Their Hardness
Different stainless steel grades have unique hardness levels, affecting their strength, durability, and applications. Hardness is measured using Rockwell or Brinell hardness scales, which help determine a material’s resistance to wear and deformation.
Austenitic Stainless Steel Grades
201 Stainless Steel – Offers moderate strength and corrosion resistance but is harder than 304 due to higher manganese content.
304 Stainless Steel – Has excellent corrosion resistance and moderate hardness, making it suitable for food processing and kitchen equipment.
316 Stainless Steel – Contains molybdenum for added corrosion resistance and has a slightly higher hardness than 304.
310 Stainless Steel – Provides high-temperature resistance with moderate hardness, commonly used in furnace parts.
Martensitic Stainless Steel Grades
410 Stainless Steel – Known for high hardness and wear resistance, widely used in cutlery and valves.
420 Stainless Steel – Offers higher hardness than 410, making it ideal for surgical instruments and knives.
440 Stainless Steel – One of the hardest stainless steel types, used in bearings and high-strength cutting tools.
Ferritic Stainless Steel Grades
405 Stainless Steel – Provides moderate hardness and oxidation resistance, often used in heat exchangers.
409 Stainless Steel – Has good heat resistance and moderate hardness, commonly used in automotive exhaust systems.
430 Stainless Steel – Offers moderate strength and good corrosion resistance, making it suitable for kitchen appliances.
446 Stainless Steel – Has high hardness and excellent oxidation resistance for extreme temperature applications.
Duplex Stainless Steel Grades
2205 Stainless Steel – Combines high strength with excellent corrosion resistance, used in marine and chemical industries.
2507 Stainless Steel – Has superior hardness and strength, designed for high-stress environments like offshore oil rigs.
Precipitation-Hardening Stainless Steel Grades
17-4 PH Stainless Steel – Provides high hardness and excellent toughness, used in aerospace and defense applications.
15-5 PH Stainless Steel – Similar to 17-4 PH but offers better toughness and impact resistance.
Each stainless steel grade has different hardness levels, making them suitable for various applications. Selecting the right grade ensures durability and performance based on environmental and mechanical requirements.
How to Identify Stainless Steel Alloy Types
Identifying stainless steel types requires a combination of visual inspection, magnet testing, and chemical analysis. Each alloy type has specific characteristics that make it suitable for different applications. Understanding these properties helps ensure the right material selection.
One of the easiest ways to identify stainless steel alloy types is by checking their magnetic properties. Austenitic stainless steel is mostly non-magnetic, while martensitic and ferritic stainless steel are magnetic. If a magnet sticks strongly to the metal, it is likely a martensitic or ferritic stainless steel type. However, some austenitic stainless steel types, like 304, may become slightly magnetic after cold working.
Another reliable method is the spark test, which involves grinding the stainless steel type against a wheel to observe the sparks. Austenitic stainless steel produces long, white sparks, while martensitic stainless steel creates shorter, orange sparks. Ferritic stainless steel generates fewer sparks, making it easy to distinguish from other stainless steel types.
A chemical test is also useful in identifying stainless steel alloy types. Using a nitric acid test, stainless steel grades with high chromium and nickel content, like 316, show strong resistance to acid, while lower-grade stainless steel types may discolour. Additionally, a molybdenum spot test can confirm if the material is 316 stainless steel, as molybdenum is absent in 304 stainless steel.
For precise identification, an X-ray fluorescence (XRF) analyzer can determine the exact composition of stainless steel types. This test detects the percentage of chromium, nickel, and molybdenum, allowing industries to verify the correct stainless steel grade. It is commonly used in quality control to ensure that materials meet required specifications.
By using these methods, manufacturers and engineers can accurately identify stainless steel alloy types. This ensures that the chosen material has the right hardness, corrosion resistance, and strength for its intended application.
Conclusion
Understanding stainless steel types helps in selecting the right material for durability, strength, and corrosion resistance. By checking quality, hardness, and alloy composition, you can ensure the best performance for your applications. Stay tuned for more insights from Sanlak, the best stainless steel manufacturer in India!