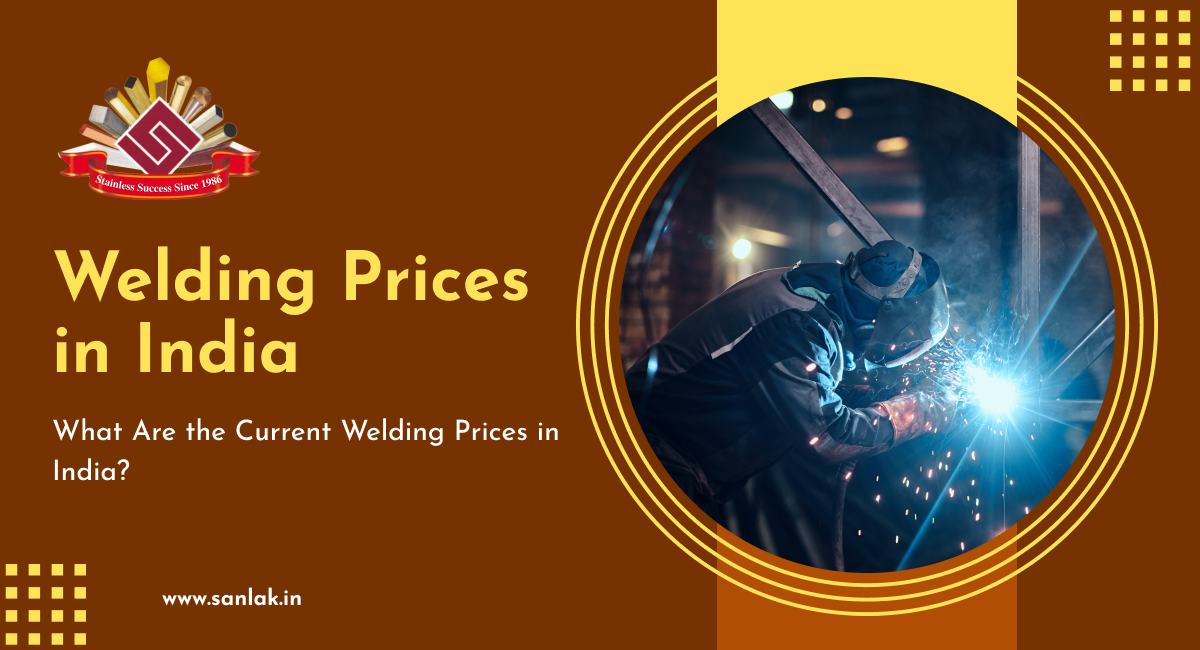
What Are the Current Welding Prices in India?
Sparks fly, metal melts, and wallets take a hit. Welding might seem expensive, but don't worry!
We're here to answer a common question: How much does welding really cost in India?
Behind every well-made metal piece, there are many factors like market prices, labor costs, and skill levels. Whether it's done in a small workshop or a big factory, welding is crucial for many industries.
So, what’s the true cost of welding?
Let’s explore the factors that determine the price and find out what goes into the final cost.
Understanding Welding Costs
Types of Welding
Welding is an essential process in many industries, and different methods can affect the overall cost. Here’s a look at some common types:
- Shielded Metal Arc Welding (SMAW or Stick Welding): A basic and versatile method using a coated electrode. It's cost-effective but requires skilled operators.
- Gas Metal Arc Welding (GMAW or MIG Welding): Uses a continuous wire feed and shielding gas. It's faster and provides better quality than SMAW.
- Gas Tungsten Arc Welding (GTAW or TIG Welding): Employs a tungsten electrode and inert gas for high-quality welds. It's more expensive and needs skilled operators.
- Flux-Cored Arc Welding (FCAW): Similar to MIG welding but uses flux in the wire, which means no external shielding gas is needed. It’s often used for outdoor welding.
- Submerged Arc Welding (SAW): Uses a submerged arc for welding, offering high deposition rates and good quality. It requires specialized equipment.
Breakdown of Welding Costs
The total cost of a welding project includes:
- Labor: Often the largest expense, influenced by the welder's skill level, experience, and hourly rate.
- Materials: Includes welding consumables like electrodes, wires, gases, and filler metals.
- Equipment: The cost of welding machines, power sources, and accessories.
- Overhead: Costs such as shop rent, utilities, safety equipment, and administrative expenses.
Factors Influencing Labor Costs
Labor costs can vary based on:
- Skill Level: Certified and experienced welders usually have higher rates due to their expertise.
- Location: Costs can be higher in urban areas compared to rural areas.
- Project Complexity: More complex or specialized welding tasks require skilled labor, which increases costs.
- Industry Standards: Compliance with industry standards (like ASME or AWS) may require additional certifications and training, raising labor costs.
Types of Welding Consumables
- Stainless Steel Electrodes
- Carbon Steel Electrodes
- Nickel-Copper Alloy Electrodes
- Stainless Steel MIG Wires
- Stainless Steel TIG Rods/Wires
- Stainless Steel Welding Wire
Understanding these factors will help you estimate welding costs more accurately and make informed decisions for your projects.
Overview of Welding Price Trends
Welding prices in India have been going up recently. This is mainly due to the rising cost of raw materials, especially metals, and the increasing demand for skilled welders. Prices can vary widely depending on where you are, the type of welding you need, and the size of the project.
Regional Price Variations
- Metro Cities: In big cities, welding costs are higher due to increased demand, higher labor costs, and a wider range of services.
- Rural Areas: In rural areas, welding is usually cheaper because labor costs are lower and there is less competition.
Comparison of Welding Prices
Here’s a general idea of welding prices. Actual prices may vary depending on the project and local market conditions.
Welding Process | Approximate Price Range (INR/hour) |
SMAW (Stick Welding) | 200-500 |
MIG Welding | 300-700 |
TIG Welding | 400-1000 |
FCAW | 250-600 |
SAW | 500-1200 |
Note: These prices are indicative and can fluctuate based on factors such as welder's skill, material costs, and project complexity.
Impact of Market Demand and Raw Material Costs
Market Demand
- High Demand: When there’s a boom in construction, manufacturing, or other industries needing welding, prices often rise because of increased competition for welders and resources.
- Low Demand: If these sectors slow down, welding prices can drop as service providers compete for fewer projects.
Raw Material Costs
- Price Fluctuations: The cost of materials like steel, aluminum, and stainless steel directly affects welding prices. When metal prices go up, welding costs usually increase as well.
- Material Selection: Choosing less expensive materials might help control costs, but it’s important to ensure the materials are suitable for your specific needs.
Finding Affordable Options
To get the best value for your welding project, consider these tips:
- Compare Quotes: Get estimates from several welding service providers to find competitive pricing.
- Project Timing: Plan your project during times of lower demand to possibly secure better rates.
- Material Efficiency: Talk to the welder about optimizing material use to potentially cut costs.
- Explore Affordable Suppliers: Look for suppliers who offer competitive prices on welding materials without sacrificing quality.
Sanlak Metals is a notable example of a company providing affordable welding products. By efficiently sourcing materials and offering competitive pricing, they can help reduce overall project costs.
Remember: While finding a good price is important, don’t overlook the importance of quality and the welder's expertise to ensure the durability and safety of your welded structure.
Factors Affecting Welding Prices
Impact of Welding Process
The type of welding process you choose affects the cost:
- Manual Processes (like SMAW/Stick Welding): These processes need less equipment but cost more in labor because they are slower and depend heavily on the skill of the operator.
- Semi-Automatic Processes (like MIG and FCAW): These methods are quicker and often cheaper because they increase welding speed and reduce the need for skilled operators.
- Automated Processes (like SAW and robotic welding): These offer high speed and consistent quality but require a big investment in equipment.
Impact of Material Type
The material being welded also affects costs:
- Carbon Steel: This is usually the cheapest material to weld.
- Stainless Steel and Aluminum: These materials cost more and need specialized welding methods, increasing the overall expense.
- Exotic Metals (like titanium or nickel alloys): These are expensive due to their special properties and the need for specialized equipment and skills.
Role of Labor Skills and Experience
The skill level of the welder impacts both cost and quality:
- Skilled Welders: Experienced welders with certifications can complete projects faster and with fewer mistakes, which can reduce costs.
- Less Experienced Welders: Welders with less experience may need more supervision and time, leading to higher labor costs and possible rework.
Influence of Market Demand and Supply
Market conditions play a big role in welding prices:
- High Demand: When more industries need welding services, prices can go up due to increased competition for skilled workers and resources.
- Low Demand: If there are fewer projects, prices might drop as welders compete for available work.
- Material Availability: Shortages or changes in the supply of welding materials can also affect prices.
By understanding these factors, you can better plan your welding project and manage costs effectively without sacrificing quality.
Tips for Cost-Effective Welding
Strategies for Reducing Welding Costs Without Compromising Quality
- Optimize Welding Parameters: Adjust settings like voltage, amperage, and wire feed speed to improve efficiency and reduce material use.
- Preventative Maintenance: Regularly maintain your welding equipment to avoid downtime and costly repairs.
- Proper Welding Technique: Skilled welders can reduce mistakes, material waste, and energy use.
Choosing the Right Welding Process
Selecting the best welding process can help save money:
- Match Process to Material: Choose the right welding method based on the material’s thickness and type.
- Evaluate Production Volume: For large-scale production, automated or semi-automated welding might be more cost-effective. For smaller jobs, manual methods could be better.
- Consider Joint Design: Design joints to be efficient, reducing the time and materials needed for welding.
Tips for Optimizing Material Usage and Minimizing Waste
- Accurate Material Cutting: Cut materials precisely to reduce waste and improve efficiency.
- Scrap Metal Management: Recycle scrap metal to recover value from leftover materials.
- Joint Design Optimization: Design joints to use less material while still being strong.
Benefits of Investing in Skilled Welders and Proper Equipment
- Increased Productivity: Skilled welders work faster and make fewer mistakes, saving on labor costs.
- Improved Quality: Better welds mean less rework and less wasted material.
- Long-Term Cost Savings: Modern equipment can be more energy-efficient and require less maintenance.
- Versatility: Investing in flexible equipment can handle different welding tasks, reducing the need for multiple machines.
By following these tips, you can lower welding costs while keeping or improving the quality of your work.
Conclusion
Welding costs in India are influenced by factors like the welding process, materials, labor skills, and market conditions. To stay within budget, consider both immediate and long-term costs, including productivity and maintenance.
For accurate price estimates and quality materials, consult experts and reliable suppliers like Sanlak Metals. Proper planning and smart choices will help you manage costs and ensure project success.